Unlocking Business Intelligence: The Rise of Process Automation in Electronics Manufacturing
This article talks about the different processes within any electronics or related manufacturing company that can be automated using AI-based tools. Heavily manual processes like trade financing documentation or accounts receivable management can now be automated up to 90% of the way using digital tools like Nanonets.
Introduction
In today's fast-paced business environment, electronics and related manufacturers face numerous challenges when it comes to managing the extensive documentation involved in their operations. From logistics and supply chain management to trade financing and human resources, the sheer volume of manual work for managing document and other related data can be overwhelming and time-consuming. Apart from this, the data is an unreadable format for most analytics tools.
They are now turning to enterprise automation tools to gather intelligence from these untapped sources of data that was until now lying dormant. Starting from automating the capture of data to transfer and finally running analytics on top of it - this is the biggest automation trend in 2023.
They say Information is advantage. Companies are slowly realising the value of the data they were ignoring until now and spending billions of dollars while building teams to arm their business units with intelligence that such data can provide.
This article talks about 7 such process automations for electronics and related manufacturing companies. With a complex global operation involving a lot of moving parts, electronics manufacturers generate a of lot unstructured data that can be a goldmine for intelligence and improving efficiency.
The Problem
The electronics industry value chain is riddled with unstructured data :
Using internal or external softwares, which are a lot of times legacy software solutions, they manage the processes from procurement to manufacturing to distribution. Each touch point generates paperwork and excel spreadsheets, stored in separate silos. Each department has analytics teams that run numbers to predict forecasts and analyse churn. Creating the dataset is a largely manual process.
Processing data manually is actually a bigger problem than you might think with a real $$ impact on a company’s bottom line.
Here are some numbers in a snapshot:
The total dollar value of the problem for the industry is a whopping $30 billion dollars. If you add the unstructured data manually transferred from various sources apart from documents (say from spreadsheets to ERP), the size of the problem easily increases by 10x.
The Solution
However, thanks to advancements in artificial intelligence (AI) and automation, companies like Nanonets are revolutionizing the way these processes are handled.
Using our intelligent AI-based transformation engine, Nanonets extracts data from unstructured sources (like documents or excel sheet), structures it and directly exports it to the correct destination.
Let us show some examples of the same process automations that can be achieved using Nanonets.
Processes That can be Automated by Nanonets
Here are the top seven processes automated by Nanonets for electronics manufacturers, enabling them to streamline operations, reduce manual labor, and increase efficiency.
Accounts Payable
Accounts payable is a critical function for electronics manufacturers. With Nanonets' AI-based intelligent document processing (IDP) tool, companies can automate the extraction and validation of data from email, invoices, purchase orders, and other financial documents. By eliminating manual data entry, Nanonets significantly reduces the risk of human error, accelerates the invoice processing cycle, and enables timely payments.
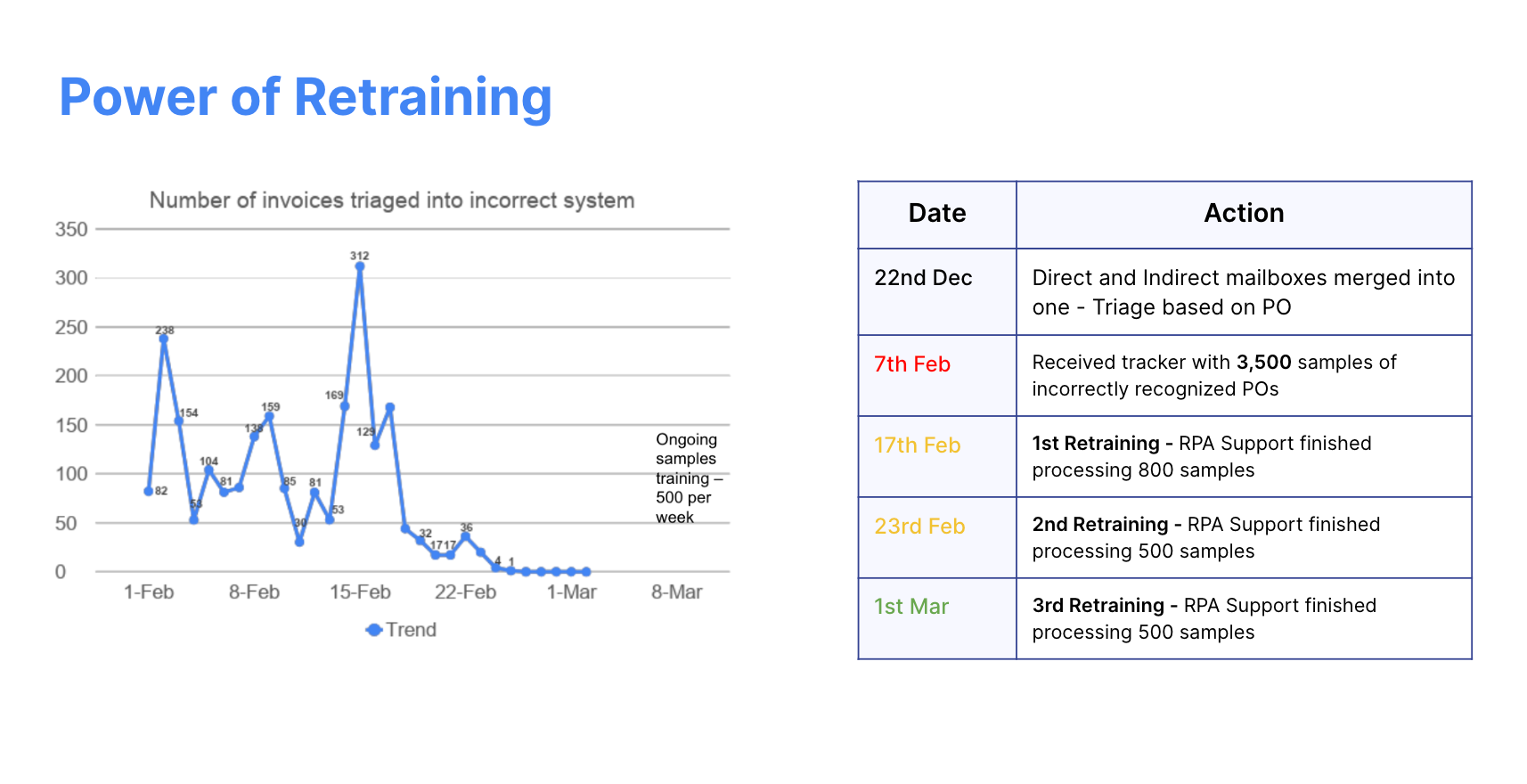
According to internal studies with live customers, implementing automation tools like Nanonets reduces accounts payable processing costs by up to 80% while improving accuracy and efficiency.
Accounts Receivable
Similar to accounts payable, accounts receivable processes can be optimized with Nanonets' IDP solution. By automating the extraction of relevant information from invoices, customer orders, receipts, and purchase orders, companies can improve cash flow management and reduce the time it takes to reconcile customer payments.
The system's high accuracy in data extraction eliminates the need for manual review, enabling finance teams to focus on strategic tasks and exceptional cases, thereby improving overall efficiency. This automation also enhances customer satisfaction by reducing payment processing times and enabling prompt responses to inquiries.
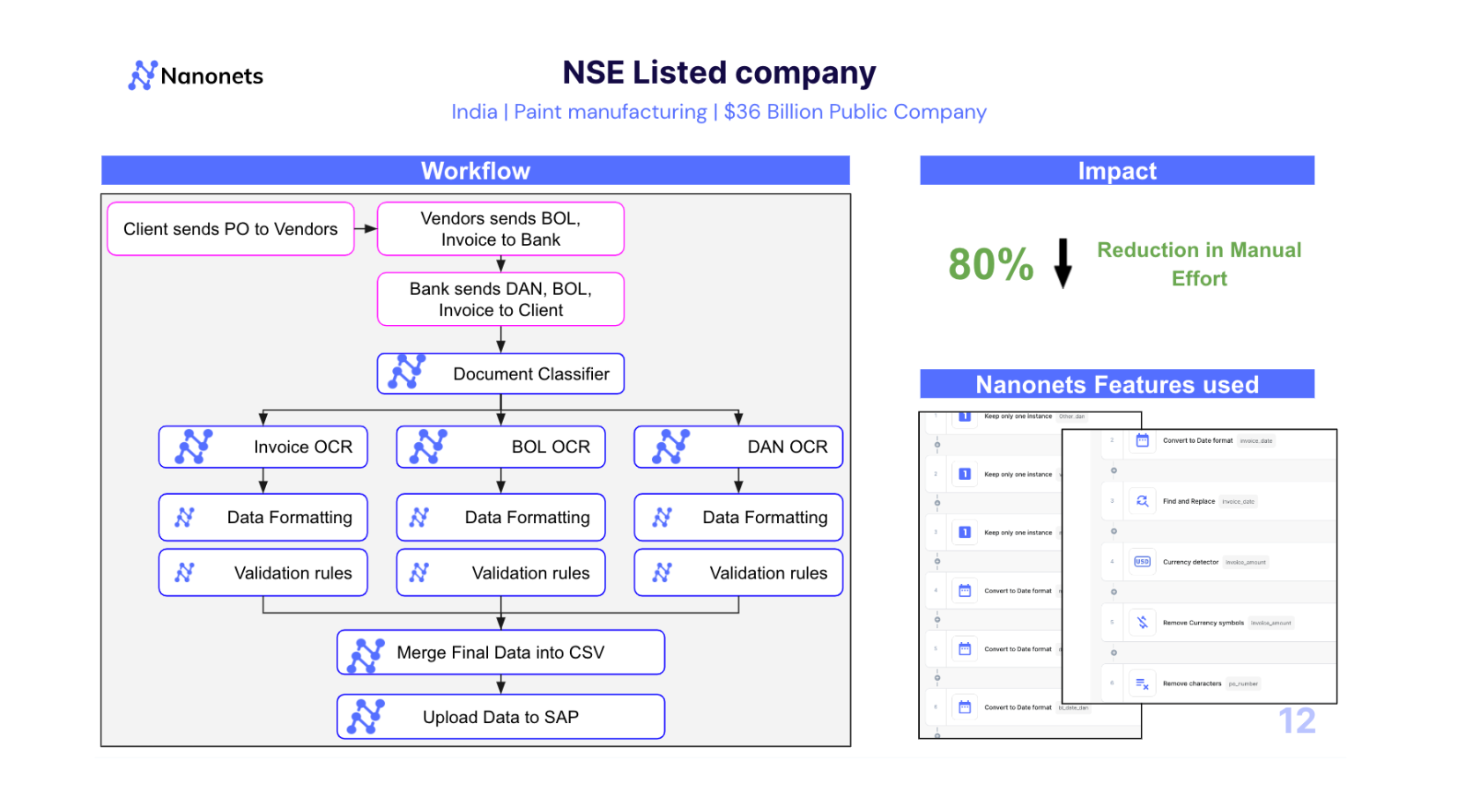
Supply Chain Management
Effective supply chain management is vital for electronics manufacturers to ensure smooth operations and timely deliveries. Nanonets' IDP tool plays a crucial role by automating the extraction of data from bills of lading, shipping manifests, and customs documents. By eliminating manual data entry and improving data accuracy, the tool enhances supply chain visibility, reduces processing time, and minimizes the risk of errors or delays.
Real-time access to accurate supply chain information empowers manufacturers to make data-driven decisions and optimize their operations. In fact, a recent survey found that companies using automation in their supply chain processes experienced a 30% reduction in lead times and a 50% decrease in inventory holding costs.

Trade Financing
Trade financing is a complex process involving various documentation requirements, such as letters of credit, bills of exchange, and purchase orders.
Nanonets' IDP solution simplifies this process by automating the extraction and verification of data from scanned documents, ensuring compliance with regulatory standards.
By reducing the time and effort spent on manual document review, manufacturers can expedite the trade financing process, enabling faster access to capital and supporting business growth. According to a study by the Institute of Finance and Management, companies that automate trade finance processes reduce processing costs by up to 70% and accelerate funding cycles by up to 50%
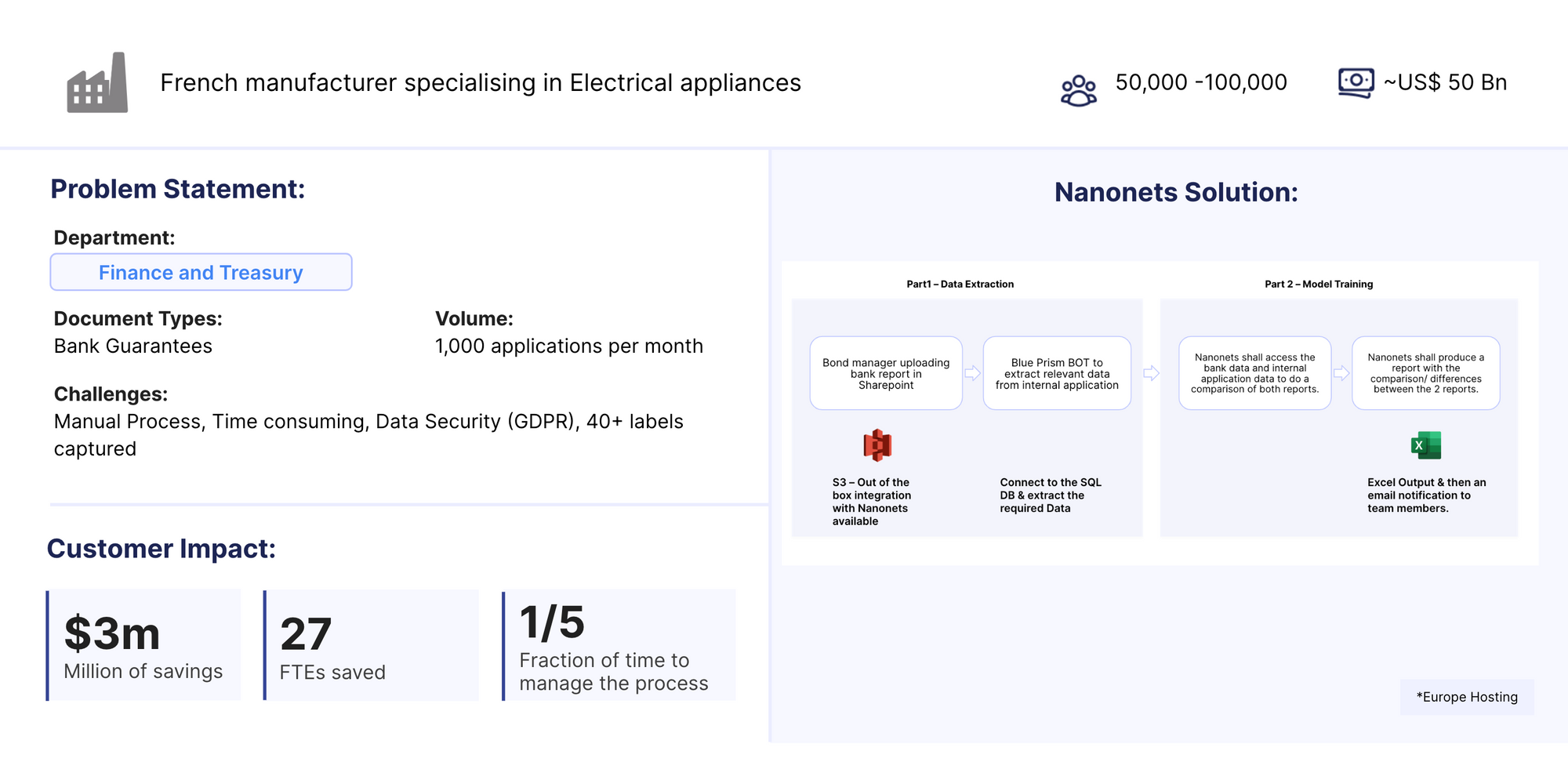
Customs Declarations
Electronics manufacturers often deal with international shipments, which require meticulous attention to customs declarations. Nanonets' IDP tool streamlines this process by automating the extraction of data from commercial invoices, packing lists, and customs forms.
By improving accuracy and reducing the risk of errors, the tool ensures compliance with customs regulations and expedites clearance procedures. Consequently, manufacturers can minimize shipment delays, mitigate penalties, and optimize their global trade operations.
A study by the World Customs Organization found that automation in customs processes can lead to a 25-40% reduction in clearance times and a 10-30% reduction in compliance costs.
Human Resources Documentation
The management of human resources documentation can be time-consuming, particularly in large manufacturing companies. Nanonets' IDP solution automates the extraction and processing of data from employee records, surveys, expense reimbursements, and forms. This automation reduces administrative burden, accelerates onboarding processes, and enables HR teams to focus on strategic initiatives such as talent acquisition and development.
Moreover, enhanced data accuracy ensures compliance with labor laws and regulations, mitigating the risk of non-compliance. By implementing HR automation tools, companies can save up to 30% of HR department costs while improving employee satisfaction and engagement.
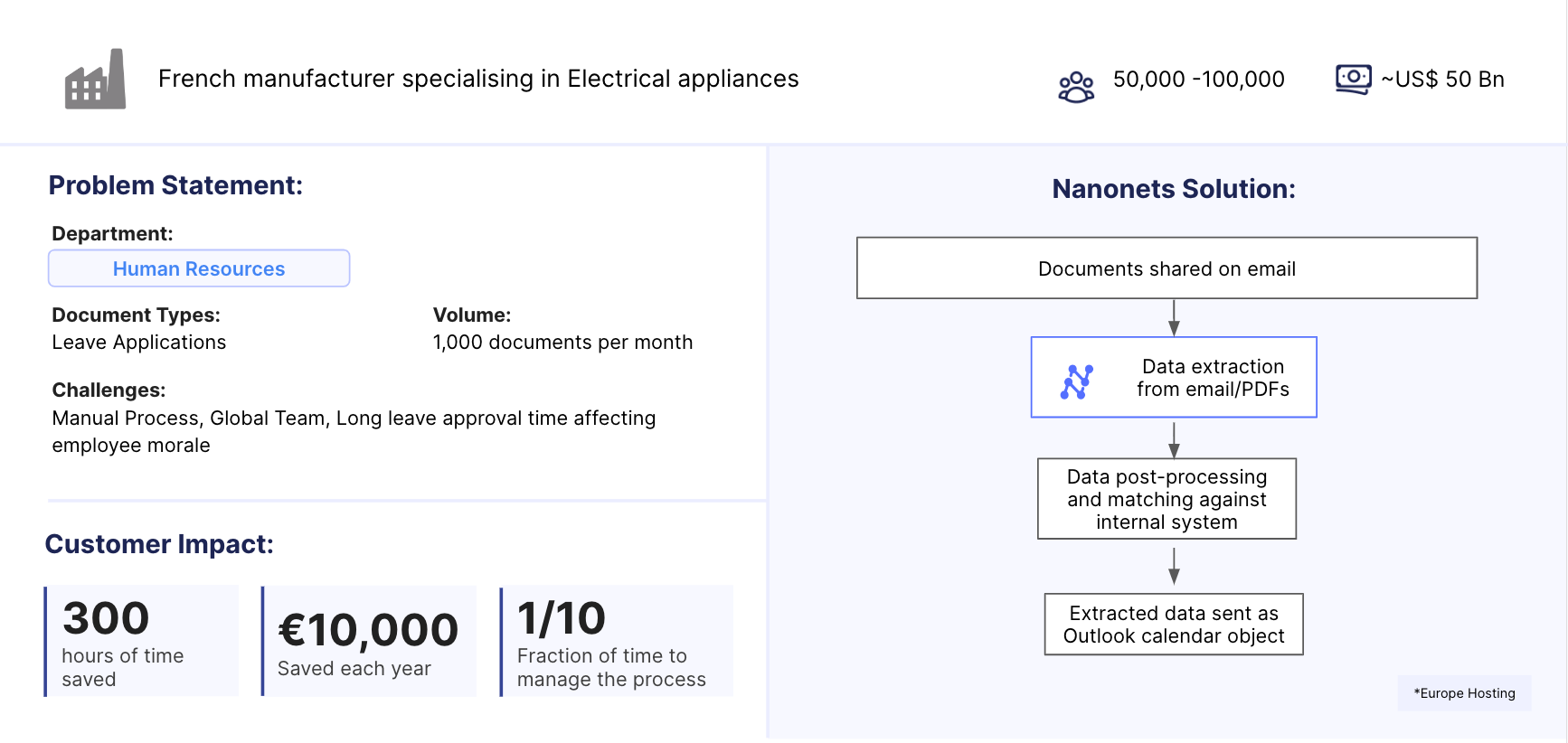
Warehouse Management
Efficient warehouse management is crucial for electronics manufacturers to optimize inventory levels and improve order fulfillment. Nanonets' IDP tool helps automate processes related to goods receipt, storage, and dispatch by extracting relevant data from packing slips, delivery notes, and inventory records. By eliminating manual data entry and improving data accuracy, the tool enables real-time inventory tracking, reduces errors in picking and packing, and optimizes warehouse space utilization.
A study conducted by the Warehouse Education and Research Council showed that implementing warehouse automation can increase picking accuracy by 30% and decrease labor costs by 20%.
Conclusion
Nanonets' AI-based intelligent document processing (IDP) tool is transforming the way electronics manufacturers handle their documentation processes. By automating accounts payable and accounts receivable processes, companies can improve financial management and cash flow. The tool's capabilities in supply chain management, trade financing, claim management, and customs declarations enable manufacturers to enhance visibility, reduce processing times, and ensure compliance. Additionally, automating human resources documentation and warehouse management processes improves efficiency, reduces administrative burdens, and optimizes operations. Through Nanonets' automation solutions, electronics manufacturers can unlock significant time and cost savings, improve accuracy, and focus on strategic initiatives that drive business growth. Embracing automation in these key processes is not only a competitive advantage but also a necessity for businesses aiming to thrive in the digital age.